ROBOTIZATION FOR ENERGY CHANGES
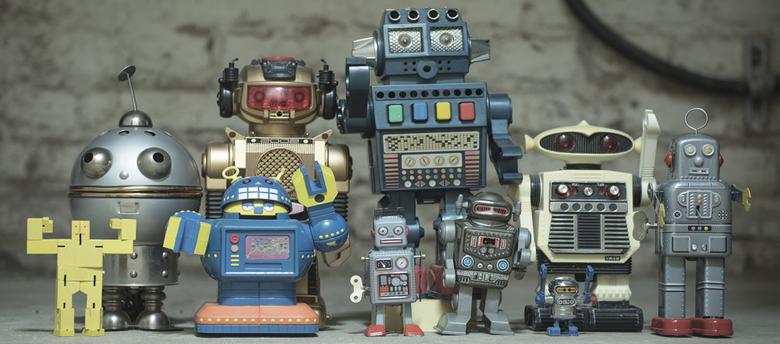
By Clarissa Strachan Content and Social Manager Quantanite
ENERGYCENTRAL- Dec 2, 2020 - The energy industry is undergoing a variety of changes. Like never before in human history, modern society is more dependent on energy, gas, water, and waste management, which places the Energy & Utilities (E&U) industry in a very unique position.
With a rapidly changing energy landscape and rising customer expectations, businesses are being forced to shift from a highly traditional, regulation-driven marketplace to an advanced technology-driven environment to keep up with the growing customer demands, the highly competitive pressure, and adding efficiencies, whilst cutting back on costs.
By incorporating new technologies and innovation, the E&U industry can improve customer service and reduce operating costs. The majority of the core processes in the E&U industry are repetitive and prone to human error, requiring a large operations team to manage the exceptions produced. However, with the application of Robotics Process Automation (RPA), these processes can be efficiently managed and completed cost-effectively.
But what exactly is Robotic Process Automation (RPA)?
RPA is essentially a software or a ‘robot’ that can be programmed to collect data and interpret it to assist an organization’s everyday operations, helping the business run more efficiently. It could incorporate analyzing data, processing a transaction, and responding to communications, among other uses, as well as removing headache-inducing tasks from the to-do lists of employees that are already stretched to capacity.
Applying RPA to your business can help improve everything from customer service to HR processes, as well as reducing costs and inefficiencies.
Many companies are beginning to roll out RPA as a steppingstone to eventual Artificial Intelligence and machine learning tools, which will undoubtedly revolutionize the future of the working environment even more than the current changes that are happening.
Several processes can be automated within any business and some of the businesses in the E&U industry are already reaping the benefits of automation. Here is a list of some business areas & processes that have been automated using RPA in the E&U industry:
- Tariff Reviews
- Billing and Collections
- Debt Collection
- Customer Services
- Customer acquisition to retention services
- Finance & Accounting
- Exception Management
- Human Resources
- Procurement
Benefits of RPA
As mentioned above, RPA can improve the efficiency and quality of service. With the robots taking care of the repetitive and mundane tasks, it takes out the robot of the humans, allowing your employees to focus on more complex and strategic tasks.
Here are some other benefits of RPA and why you should think about implementing RPA in your organization now:
- More efficient lower cost transactions
- Robots are found to be quicker than the human workforce and can be easily scalable at short notice compared to hiring additional employees
- Improvement in data accuracy with robots making no mistakes
- They leave an audit trail and can provide complete traceability
- Reduces security risks with limited human access to sensitive data
- Robots can work 24/7, they do not need breaks, holidays, or sick leave
An RPA virtual workforce will free up your talented resources for customer engagement and value-added tasks by automating your business-critical processes. It is already noticeable that early adopters of RPA are already reaping the benefits that the technology can provide.
Over the last few months and the uncertainty which COVID-19 has brought, businesses that had already implemented RPA benefited from the technology when organizations made changes to their work- force and processes to enable them to work from home and still keep up to the demand
How to Begin Your RPA Journey
Beginning your RPA journey is not easy. As with any innovation, an organization needs to first test the technology on a small scale in order to evaluate the suitability for their needs and better identify the benefits which it may add before making a large investment decision. To effectively do this, you can run a small pilot project by automating one of your business processes.
We have seen too many organizations begin with automating their pain points or even selecting the most difficult process to automate, assuming the rest of their RPA journey would be a lot smoother. When running a pilot program, you want to ensure that the process you have chosen will be able to demonstrate the value of RPA and not bury you in development or process re-engineering.
Below are 8 key features of a good candidate for the RPA pilot:
1. Start small
You should start by selecting a relatively small process that will allow you to build up knowledge and required capabilities before scaling up. The identified process should be relevant to your business goals and bring benefits to your organization. Avoid picking a large process, as it would extend the pilot program timelines and make the overall project a lot more complex than it should be for the initial pilot.
2. Low Complexity & Level of Effort
The pilot process should require a low level of effort. Avoid selecting a process that is too complex, as that would increase the risk of causing delays due to the different types of exceptions.
It is recommended that you consider the below points when evaluating the potential of a pilot process automation:
- Number of steps which the process has
- Number of applications which the process utilizes
- Number of business exceptions
- Structure & quality of data
- Volume of transactions
3. Standardized Process
The process you select should have well defined & documented rules and procedures. A robot is only as good as the script that you tell it to execute, and the RPA developer will need the process broken down at the keystroke level so that they can train the robot to follow the process as a human would.
You should dedicate at least one lead SME to dictate the design for the robot, as they work on the process manually day in day out and will have the full depth of the process including any challenges they face, rather than the process owner. Choosing a process that is not standardized will only lead to more hurdles down the road.
4. Simple Integration
When selecting a process for RPA, you need to weigh out whether the process is suitable for RPA or, whether you could achieve the desired results using an API integration. If your process only requires defined transactions between two applications, then API may be your best bet. The majority of the time, it is not this simple, and RPA will be your solution but when selecting a process for the RPA pilot, ensure other automation possibilities are not more suitable before making the final call.
5. Connectivity & Stable Systems
One of the key factors for a pilot process should be working with applications that are either window-based or browser applications. When you are selecting a pilot process, it is best to avoid process- es that would need to interact with a virtual environment such as Citrix, as the developer would need to utilize surface automation techniques. The RPA developer should also perform an application assessment for all of the applications related to the process so that they can identify any potential issues such as the stability of the ap- plication, or not have an upgrade due to name a few.
6. Structured & Digitized Data
An RPA pilot process needs to be kept simple, avoid using unstructured data, scanning documents, or information that is not digitized as you will need to integrate other AI technologies. The input data can come directly from an application or even an Excel file for example but ensure the data is structured so that the robot knows exactly where to pick up the information from. There are many ways of get- ting information out of PDFs, scanned documents, and other files but for the pilot process, you should stick to structured & digitized data.
7. Testing
Another important factor to have a successful RPA pilot is testing. Testing can seem daunting, but it will pay off, testing would happen at many stages of the project such as during configuration, User Acceptance Testing (UAT) and during deployment. To ensure you have a successful RPA pilot, the RPA developer should thoroughly test each component of the RPA solution during configuration and then run end-to-end testing before handing it over to the business to perform UAT. UAT is the chance to try and break the solution as this will limit the chances of the RPA solution breaking in production. You should test the process with enough test cases to cover the happy path and any exceptions the process may face to ensure the robot would handle the scenario appropriately. During deployment, it is advised to start off small by only working a few transactions and validating the results and then ramp up incrementally to a full deployment once you are happy with the results.
8. Business Value & Setting Clear Goals
In many cases when an organization starts its automation journey with RPA would have heard some fantastic claims of ROI and cost-saving numbers. Whilst this is possible and can be achieved, these should be included when you are prioritizing automation projects, but it is not essential for the RPA pilot process. For the pilot process, you can consider ROI but it should not be the only factor, it should be important what the organization is specifically trying to achieve and there is no right or wrong answer. Some of the most common objectives that we see outside of ROI & cost savings are:
- Improve employee satisfaction & experience
- Improve quality and risk compliance
- Improve revenue
- Innovation
Although there are no rules on how to choose the correct pilot process, these tips should make life a little bit easier and increase the chances of a successful RPA pilot program. The RPA pilot program will set the stage for an enterprise-grade program so it is important to prove success early and selecting a process that is a good fit for your program will get you off to a strong start on your automation journey.
3 Simple Steps to Scale up Your Program
Once you have successfully completed the RPA pilot program, to realize the maximum potential of RPA, businesses should use the following approach:
1. Assess the requirement
Organizations should start by analyzing their current processes and checking their suitability for RPA, with some of these criteria having been highlighted above. You should then shortlist the various processes based on the organization’s objective or operational issues that RPA can address efficiently and effectively, whilst assessing the impact, benefits, and feasibility of the automation.
2. Build a business case
Build a business case to show the comparison of costs involved to build & maintain the RPA solution versus the various benefits associated with automation. The business case should include the cost of the resources required, software licenses, hardware, to name a few, and the benefits.
3. Choose the right model
There are several RPA vendors on the market, and the top 3 leaders are Automation Anywhere, Blue Prism, and UiPath. There are also many consultancies out there who can help you with implementing RPA. You should find the right partner who can provide an end-to- end RPA implementation service and provide further support to maintain the robots if required.
Top Mistakes to Avoid When Implementing RPA
With RPA promising return on investment anywhere between 30% to 300% within the first year, it is a no brainer that organizations are implementing RPA. However, not all news is great news and with RPA it has a 30-50% failure rate on initial projects. Over the years, we have acknowledged the most common RPA mistakes that we see organizations make and here are the top 8 mistakes you should avoid and enable your organization to implement Robotic Process Automation successfully.
1. Not engaging senior executives
For RPA implementation to be successful, you will need to secure a strong leadership team from both the business and IT departments in your organization. The business leaders will need to be on board so that they can free up resources such as subject matter experts (SMEs) and ensure that you get everything you need on time during the project such as process knowledge, metrics, and test data, just to name a few.
The IT leaders should also be involved from early on in the project too as RPA relies both on IT infrastructure and IT applications. The IT team will be able to quickly highlight & resolve any unexpected issues or challenges along the way, such as IT software or infrastructure upgrades, issues with IT security policies and relevant access for the robots.
2. Automating bad or broken processes
Automating a bad process is like speeding up a bad process, it is recommended that you analyze the processes and streamline them where possible before automating them. Streamlining the process has many benefits such as, it will make it a lot easier to automate as it will have a simpler decision logic, you will need to test less scenarios during User Acceptance Testing and it will be easier to maintain once the automated solution is in production.
3. Not having a dedicated team
You will need to plan and have dedicated valuable resources avail- able when required during your project as any delays will affect the return on investment (ROI). For example, you will need some dedicated time from SMEs and other stakeholders such as the process owner for requirements confirmation, solution design, testing, and deployment and this can be challenging as they still have their day- to-day workload to manage.
4. Overcome the fear of digital workers
When talking about bots with organizations, it is naturally assumed that bots will replace humans and organizations face a lot of resistance to automation from the business. It is important to introduce RPA and educate employees upfront about how RPA would benefit them.
The robots would automate the boring repetitive tasks whilst freeing up the employees to work on value-added tasks such as customer service and other strategic work requiring human attention. It is crucial that there is an introduction to RPA and the organization’s objectives and there should be an ongoing communication with the employees so that they are aware of how the automation will be impacting them.
5. Lack of coordination with the IT team
Implementing RPA without coordination with the IT team is a mis- take we see day in day out. This is one of the most critical mistakes you can make, as you will be using the IT infrastructure and various IT applications for RPA. Having IT onboard will make it easier to scale up your efforts and leverage each other’s expertise to automate solutions simpler, securely, and safely. In the past, we have seen IT teams delay ROI on automation as the information security risk assessment has not been completed, the correct infrastructure is not in place or they put a pause until performance testing has been completed to check that their infrastructure can handle the speed of the bot navigating through applications as we have seen in the past, without testing, the robot has taken down the IT application servers causing business-wide disruptions.
6. Insufficient process testing
Thorough testing throughout the project is vital and cutting corners or assuming that the solution will work in different environments is one of the many mistakes that an organization can make. You will need to test the solution on Development, testing, and production environments to ensure there are no differences between these environments.
As we know, the bots can handle the different process flows as long as they are programmed to manage them and you will need to test the “happy” paths as well as the exceptions to ensure that the robot will be able to handle the scenarios. Involve your SMEs from the be- ginning so that they can help you define the testing scenarios and also collect the test data upfront so that it doesn’t slow your project down as it can be difficult to collect test data if there isn’t sufficient data available.
7. Roles & Responsibilities
Most of the time organizations tend to forget that there will be maintenance required after the automated solution is live in production or they assume that the robots will take care of themselves. You will need to ensure that you have adequate resources to manage the robots in production, which can include anything from scheduling the robots to all the way to supporting & maintaining the solutions. As we know the processes can change or the application involved will have a roadmap of changes.
8. Failing to scale up
Deploying the first robot is easy, but many organizations fail to scale up their efforts beyond that. The true benefits of RPA can be reaped only if you automate the right set of processes. In order to scale up your efforts, your organization will need to create an RPA Center of Excellence (CoE). The RPA CoE is a pool of capabilities that is required to drive all the functionalities of an RPA initiative including some of the following:
- Building RPA expertise in the organization
- Acquiring and training new resources
- Seamless change management
- Establishing clear standards, procedures, and policies
- Ensures that compliance regulations, information security requirements, and regulatory standards are met
- Oversees RPA technology infrastructure
- Evaluates automation opportunities and prioritizes them
Having an RPA CoE in place will allow your organization to be self-sufficient and constantly identify automation opportunities all the way to supporting a large bot ecosystem. The RPA CoE will also allow you to maximize the benefits of the ever-evolving scope of intelligent automation products.
Conclusion
In the highly competitive utility business, energy firms cannot just lean back and maintain the status quo. RPA has been the answer for many organizations over the past few years allowing them to take their step towards digital transformation. We often still see a large part of a highly educated workforce wasting their time in executing repetitive and rules-based tasks. Now is the time to open this pool of creativity by automating these tasks and allowing them to be focused on value-added tasks such as customer service to gain a competitive advantage over competitors.
-----
This thought leadership article was originally shared with Energy Central's Digital Utility Community Group. The communities are a place where professionals in the power industry can share, learn and connect in a collaborative environment. Join the Digital Utility Community today and learn from others who work in the industry.
Earlier:

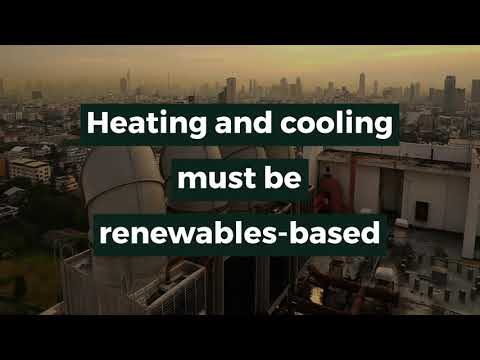
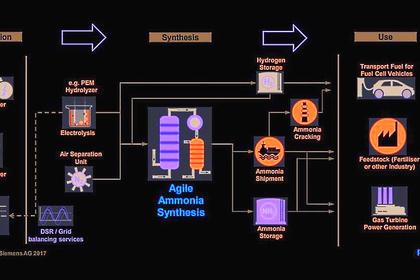



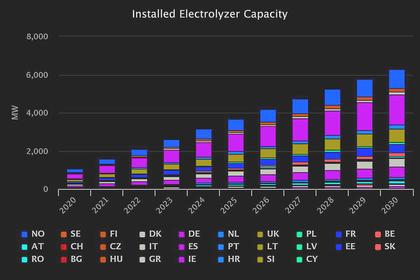