3D-PRINTED MICRO NUCLEAR
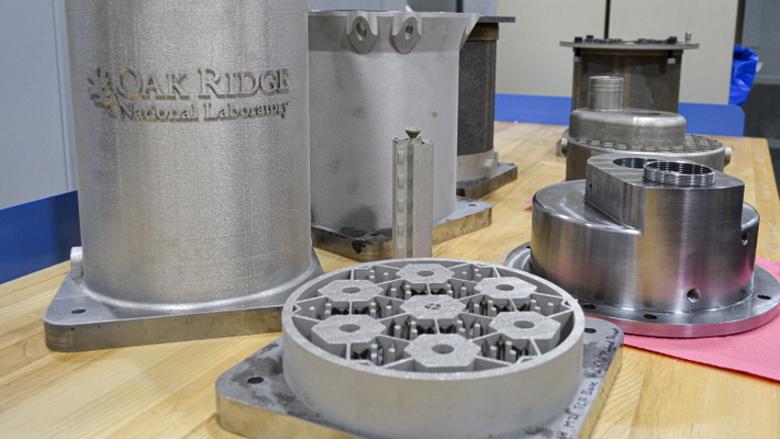
WNN - 12 May 2020 - Researchers at the US Department of Energy's Oak Ridge National Laboratory (ORNL) are refining their design of a 3D-printed nuclear reactor core, scaling up the additive manufacturing process necessary to build it, and developing methods to confirm the consistency and reliability of its printed components.
ORNL launched the Transformational Challenge Reactor (TCR) Programme in 2019 with the goal of designing, manufacturing and operating a demonstration additively manufactured microreactor by 2023. The programme leverages advances from ORNL in manufacturing, materials, nuclear science, nuclear engineering, high-performance computing, data analytics and related fields. ORNL said. TCR will introduce new, advanced materials and use integrated sensors and controls, providing a highly optimised, efficient system that reduces cost, relying on scientific advances with potential to shape a new path in reactor design, manufacturing, licensing and operation.
"The nuclear industry is still constrained in thinking about the way we design, build and deploy nuclear energy technology," ORNL Director Thomas Zacharia said. "DOE launched this programme to seek a new approach to rapidly and economically develop transformational energy solutions that deliver reliable, clean energy."
The TCR programme has completed several foundational experiments including selection of a core design, and a three-month "sprint" that demonstrated the agility of the additive manufacturing technology to quickly produce a prototype reactor core. Researchers will now focus on refining the selected design and the processes that will ensure an optimal and reliable energy system.
The TCR core will be advanced manufactured and housed inside a conventionally manufactured and qualified vessel made from grade 304H stainless steel. The core consists of uranium nitride coated fuel particles within an advanced manufactured silicon carbide structure. The fuel blocks are arranged within advanced manufactured grade 316L stainless steel structures and are interspersed with yttrium hydride moderator elements. The hydride moderator minimizes the amount of high-assay, low-enriched uranium required to reach criticality. The reactor system will be housed inside a vented confinement within an ORNL building. TCR will be the 14th nuclear reactor to be built at ORNL.
"We have been aggressively developing the capability to make this programme a reality over the last several months, and our effort has proven that this technology is ready to demonstrate a 3D-printed nuclear reactor core," said Kurt Terrani, the TCR technical director. "This is a foundational effort that can open the floodgates to rapid innovation for the nuclear community."
As part of deploying a 3D-printed nuclear reactor, the programme will also create a digital platform that will help in transferring the technology to industry for rapid adoption of additively manufactured nuclear energy technology.
"The entire TCR concept is made possible because of the significant advances in additive manufacturing process technology," Terrani said. "By using 3D printing, we can use technology and materials that the nuclear community has been unable to capitalize on in the last several decades. This includes sensors for near autonomous control and a library of data and a new and accelerated approach to qualification that will benefit the entire nuclear community."
ORNL is partnering with Argonne and Idaho national laboratories and engaging with industry to enable rapid adoption of the technology for commercial use. BWXT is providing manufacturing support to the programme in addition to uranium oxycarbide tristructural isotropic (TRISO) fuel.
-----